Environmental Solutions
Brands and retailers alike are under tremendous pressure to demonstrate their sustainability credentials with increasing consumer awareness of packaging and labelling environmental performance. Consumers are seeking not only high quality goods with convenience today; they also want to feel good about what they buy. As such, retailers need to respond with new, innovative solutions to their packaging and labelling of products and promote their environmental credentials.
As a global label manufacturer, SATO is committed to becoming the leader of innovative environmentally friendly label solutions to support customers’ sustainability strategies. Whether recyclable or compostable, including renewable content, linerless or plastic free… SATO offers a range of environmentally friendly label solutions to meet customer needs and support them on their journey to responsible business.
Short shelf life solutions
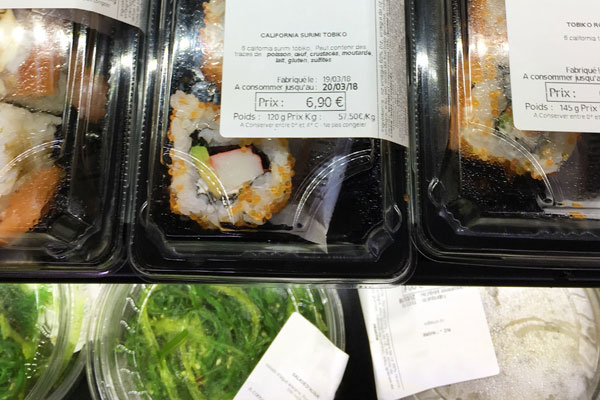
With the increasing pace of retailing, and consumer demand for fresh, high quality products, retailers are challenged to expertly manage their expiration dates to minimise waste and costs. Accurate documenting and communication of expiration dates are key to retailing efficiency and profitability. Automation of the identification, data collection and labelling processes increases visibility and accuracy to help drive down losses.
When there’s no room for error, count on SATO products to accurately communicate expiration dates. Grocery stores and restaurants know the difficulties of food rotation and impact of wasting expired items. Handwriting labels takes time and training, and is prone to errors. SATO can help make expiration date marking easy and automated.
With a comprehensive range of mobile, desktop and industrial printers, software and labelling solutions, SATO customise the labelling process to meet a wide range of retail needs.
Designed for small retailers and convenience stores that do not have ERP or database management solutions, ‘Label Over Barcode’ solutions improve the way stores handle perishable and short shelf life goods and are ideal for managing end-of-line discounting. A ‘sandwich’ label, with a clear film laminated underneath the top substrate, is placed over an item’s barcode to stop it being scanned at the till. When the item reaches the checkout, the till operator removes the label, scans the product and inputs the reduced price manually. This process can also be adapted for non-EPOS terminals by entering the lower price as the price of the item.
‘Barcode Over Barcode’ labelling means placing a new barcode label with the reduced price information over the top of the existing barcode. This enables handling time to be substantially reduced - leading to improved checkout efficiency and customer service.
The new label is simply placed over the existing barcode and shows the original price, the reduced price and a ‘Code 128’ barcode. This new barcode contains the original product article number and the reduced price. When the till operator scans the item the customer is automatically charged the reduced price and inventory records for the store are automatically updated.
See SATO Solutions
Food waste management
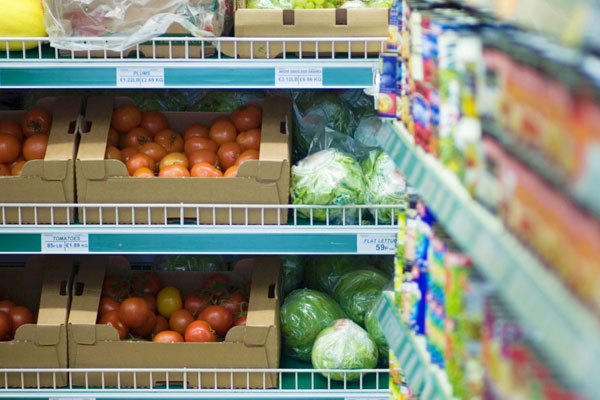
With food waste set to top 88 million tonnes annually, with associated costs estimated at 143 billion euros according to the EU, finding solutions to minimise food waste in the retail sector is a key concern of retailers today. Retailing is said to contribute up to 5% of overall food waste volume in the EU. It is therefore a key part of many retailers’ sustainability strategy to optimise labelling and expiration date management, as well as looking at ways to redistribute through food banks, charity and community projects.
Real time data for real time management of waste
At SATO, we know labelling is a brilliant communication tool but getting it wrong can be disastrous to food waste creation. Incorrect bar codes, cans with ripped labels, or products with out of date seasonal labels, all create product waste and have to be reduced to clear or discarded as they are not considered fit for sale. There is also often consumer confusion over labelling safety instructions - ‘sell by’, ‘use by’ and ‘best before’ being classic examples. These are all scenarios where SATO can support retailers to address waste by providing real time data on the condition of the product to manage stocks effectively.
Retailers know that shelves need to look full in order to make products more attractive to shoppers but this brings challenges in inventory management. From a shopper perspective, later expiration dates mean a product is fresh, where as close to the date means the product is deteriorating. This leads to the need for effective stock rotation as well as markdowns on the last day a product can be sold.
For most supermarkets, scanning barcodes to determine how much stock is in the system near to expiration, and then calculating a new price to encourage sale, is standard practice; the more stock at issue, the lower the price.
Utilising a SATO mobile wireless label printer, which can communicate with the scanner, means that product pricing can be reduced based on real-time information i.e. if products are still not moving, the price can be reduced further with quick on-demand printing of new labels and barcodes at the store shelf.
Labels = communication AND education
The label is a powerful communication tool and can be used to educate customers - enabling them to make more informed choices. Whilst less than 5% of food waste resides in the supermarket, over 50% of waste happens in consumers’ homes. The label provides a great opportunity for retailers to educate their shoppers on food waste, freshness, recycling and how to use certain products after their ‘best before’ date.
Labels can be customised with smart technologies - barcodes and QR codes - that the consumer can scan with their smart phone to pick up helpful advice, hints and tips on saving waste (and money), understanding sell by / use by dates, as well as recipes and recycling.
SATO, a leader in labelling technology, understands that food waste management is a complex problem and there are no simple answers to big problems. However, applying the technology and expertise gained over many years, SATO can support retailer operational efficiency and help the planet!
Find out how we partnered with Comerso to help combat food waste with sustainable labelling solution
See SATO Solutions
Linerless labels
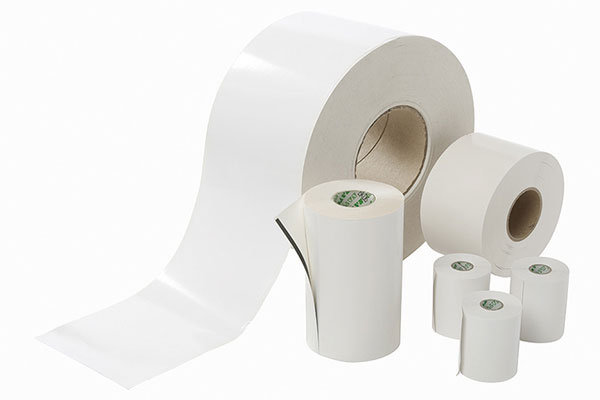
Lower label waste processing costs by using linerless
Unlike conventional labels, the SATO range of Linerless Labels are not carried on a backing paper. These pressure sensitive labels are wound on a roll that has release coating applied to the front of the face stock to prevent the adhesive from sticking on to the label below. The range comes in a selection of face stocks, which include standard paper, direct thermal and a choice of permanent, re-positional or removable adhesive strengths. Linerless labels are particularly suited to mobile printing solutions.
More labels, less waste
Because linerless labels do not come with a backing liner, customers receive more labels on a roll - up to 40% more in fact. Which in turn, saves on storage space and the time needed to change empty rolls.
The increased number of labels per roll results in a lot less waste. SATO has completely eliminated the need for the disposal of liners. Waste, in the form of liners, accounts for a considerable amount of silicone going to landfill, so choosing linerless labels lessens the label carbon footprint and removes a potential safety hazard from retail floors.
Lowering the cost of ownership
Overall, an investment in linerless labels is one that will pay dividends. Increased efficiency, combined with strong environmental credentials, helps to reduce costs both directly and indirectly.
See SATO Solutions

Contact us
