Warehousing & Distribution Management
SATO seeks to ensure the smooth and efficient flow of products and information from goods receipt to inventory management and shipping, as well as effectively managing the returns process, where required. SATO saves business time, cost and waste through enhanced visibility, productivity and efficiency.
Continual monitoring and visibility of goods, integrated into each operational area and business function, supports businesses to drive efficiency, productivity and streamline operations. With customer compliance and profitability at the forefront of SATO solutions, SATO designs agile, flexible smart solutions to support businesses from goods receipt to inventory management and shipping, as well as effectively managing the returns process, where required.
SATO Visual Warehouse
SATO developed Visual Warehouse™, the industry’s first wearable navigation system intended for use in logistics centers that combines barcodes and RFID with virtual 3D mapping and indoor locating technologies.
Visual Warehouse™ can locate objects with greater precision - within a 30 cm margin of error - than conventional locator systems, with the help of wearable devices that navigate the worker to items using three-dimensional maps and voice guidance. The system facilitates receiving operations at warehouses that manage inventory in random locations, to improve efficiency in inventory management, speed up shipments by instructing the shortest route, and realise inventory/shipping management suited to the characteristics of each product.
With a remote support feature that instructs the shortest route to a product with easy-to-understand voice guidance such as, "Two more metres to your desired product," "Turn right at the next aisle," or "Changes were made to the type and volume of products to ship," the system helps with labour savings for shipping and improves quality of operation independent of worker experience level.
For more information about Visual Warehouse™, please get in touch with a member of the SATO team
Intelligent warehousing and distribution management
SATO solutions integrate seamlessly with warehouse management systems, incorporating data collection and wireless functionality to facilitate real-time awareness of locations, quantities, conditions, origins and destinations of products. Automation of the entire process flow eliminates manual, inconsistent human intervention from receipt to shipping and delivers best in class compliance and safety for optimum business performance.
SATO provides a range of solutions for the following warehousing and distribution requirements:
Receipt of goods
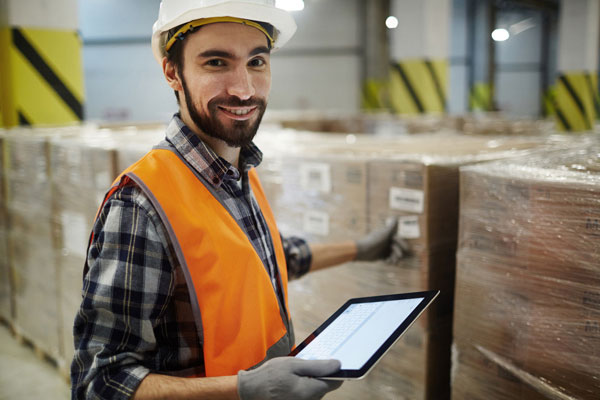
In a perfect world, goods arrive in pristine condition, accurately labelled and ready for immediate storage. The reality, even with digital communications and modern transportation systems, is that damage occurs in transit, incorrect products or quantities are shipped and human error interferes with what should be a smooth receipt process.
Errors can happen but this does not need to impact business performance if handled with the latest technology solutions from SATO.
SATO offers a broad portfolio of intelligent solutions to quickly and efficiently manage inbound goods and materials. Identifying and verifying goods with barcodes and RFID tags, SATO best in class identification solutions enable real-time data capture and business intelligence in the goods-in department.
Reconciling orders with delivery notes and packing slips to quickly sort products and move to inventory, SATO mobile, desktop and industrial print solutions create operator efficiency and enable customers to remain lean and competitive.
See SATO Solutions
Storage and replenishment

Storing and replenishing depleted goods in the busy distribution and warehouse environment can quickly get out of control if not managed accurately and efficiently by an integrated intelligent warehouse management system.
Ensuring receivables are in the right location, at the right time, and rotated correctly to create efficient selection, is front of mind for operators balancing time, cost and customer service.
Getting product logistics right supports an entire business operation. Accurate product flow information enables purchasing and manufacturing processes to be optimised. Aligning inventory levels to service commitments, balances cash flow requirements and drives customer satisfaction. All of these strategies rely on accurate real-time data availability to manage incoming goods, picking, cycle counting and the reorder process.
SATO supports warehousing and distribution operators with a range of technology solutions to ensure optimal inventory levels are maintained, real-time data collection is available and effective decision-making can be enacted in the business.
SATO enables efficient working whether unloading transport or on the warehouse floor - constantly connected, always accurate, and always available.
See SATO Solutions
Inventory management
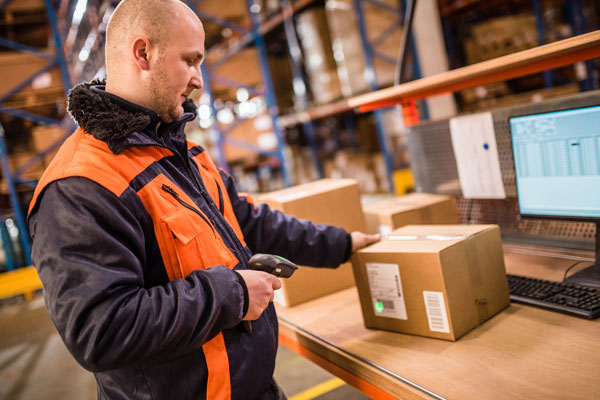
Modern inventory management involves warehousing and distribution companies applying five key processes to their business:
- Effective demand forecasting
- Efficient warehouse flow
- Appropriate inventory turns/stock rotation
- Cycle counting
- Process auditing
Truly understanding the market and business environment is paramount to being able to manage these processes effectively. However, knowing the current status of all goods, assets and employees within the business can make the difference between success and failure. Shrinkage, loss and misuse, as well as lack of visibility of where and how inventory is being used, can result in excessive costs and the inability to service customers.
SATO, a leader in auto identification and data collection solutions for the transport and logistics sector, understands the competitive nature of storage and distribution. It works closely with its customers to understand their unique needs and requirements to tailor intelligent solutions to their challenges to drive performance and profitability.
From mobile warehouse inventory management systems to RFID tagging of goods, SATO understands how to enhance warehousing and distribution processes to adding value and efficiency to any situation.
Streamlining inventory management processes to achieve more from less, optimising labour and removing human error, is core to SATO’s philosophy.
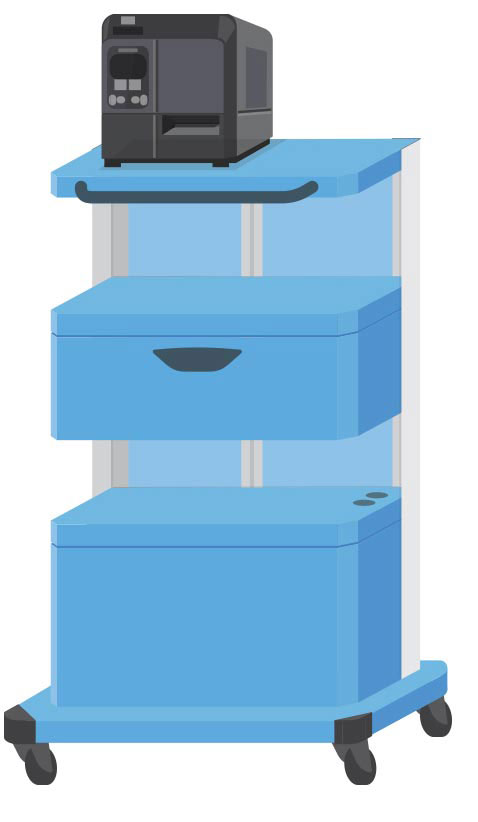
Trolley System example
A mobile printing station for the warehouse environment, a wireless trolley system provides a low cost, reliable and flexible solution to inventory control, shipping and checking operations. It reduces operational downtime as operators can print there and then, on site, any time.
A robust, steel-framed trolley with integrated thermal barcode printer, mobile battery, power supply, scanner and wireless LAN tools, the trolley can also mount a PC, keyboard and standard office printer to enable connection to the host CPU or other equipment. Constantly connected, flexible and mobile, the Trolley System enables document printing, anywhere in the warehouse, at any time.
See SATO Solutions
Real time location management
The pace of business is accelerating in a variety of sectors, from transport and logistics to healthcare and retailing. Companies wanting to maintain competitive edge need to respond quickly to the changing business environment, trends and seasonality.
The tracking of goods, assets and people is therefore becoming more important in managing a business, as real-time, speedy decisions must be made and accurate processes implemented.
SATO understands that real-time visibility of assets and employees is critical to business performance and offers a range of tailored technology solutions to provide higher visibility to manufacturing, logistics and general business processes that make the difference to warehousing and distribution management.
SATO RTLS is a tailored logistics solution using Bluetooth Low Energy (BLE) technology to collect data from tagged goods, transmitting information back to a company server in real-time. Cost effective and delivering real time information about precise locations in the warehouse, the location scan is updated every 2 seconds on the premises and has a wide coverage of up to 10m.
SATO offers a range of transportation and logistics technology solutions to identify, track and trace goods whilst complying with the latest regulations regarding labelling, safety and security. Including barcode and RFID ready printing solutions, SATO empowers transport and logistics companies to manage their expanding business requirements without disrupting the entire business infrastructure.
See SATO Solutions
Product picking and assortment
Efficient picking and assortment relies on accurate, up-to-date information at all times on the availability of stock and latest demand requirements. Operators wanting to deliver enhanced supply performance to their customers need high productivity, reliability and cost effective operations in the warehouse. SATO, a leader in auto identification and data collection solutions for the transport and logistics sector, understands this and designs integrated tailored solutions to meet these needs.
SATO Visual Warehouse
SATO’s Visual Warehouse is a wearable navigation system that streamlines storage, picking and route navigation by combining barcodes with virtual 3D mapping and high-precision indoor positioning technology.
The Visual Warehouse solution utilises an algorithm that has been designed to guide picking personnel on the shortest possible route, with audio and visual instructions and voice control for verification. Ideal for streamlining labour utilisation and inventory management, Visual Warehouse helps to improve operational efficiency in logistics scenarios.
The solution utilises three elements, a real-time location system, 3D mapping software with shortest route algorithm, and smart devices. Virtual 3D map data and simulated route data is collated, processed and communicated to users in real time via smart devices. Voice recognition technology provides a ‘hands-free’, ‘eyes-free’ and ‘process-free’ picking operation, which enhances productivity and accuracy by eliminating wasted time when searching for items.
Mobile printing system for picking labels
This system uses wireless hand held terminals and rugged mobile printers to print both picking labels and/or shipping labels to improve the picking and checking operations in the warehouse environment.
On demand, on site labelling with wireless print capability enables an increase in response times, productivity and efficiency reducing costs in the picking and checking operations.
See SATO Solutions
Packing and preparation
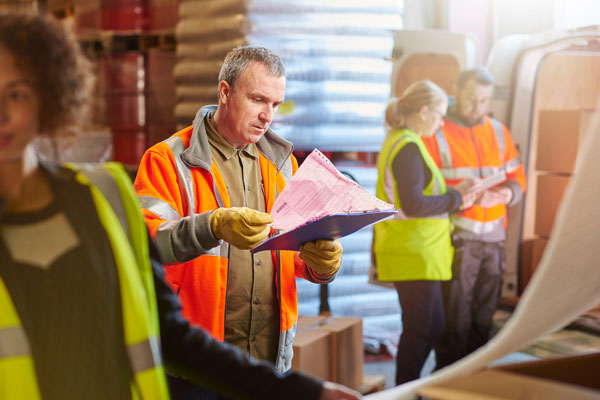
Despite all the best efforts of an efficient manufacturing process, the final packing and preparation of goods for shipment is a key stage of warehouse operations. If not handled correctly, mistakes can result in increased costs, waste, missed service level agreements and ultimately impact customer service.
Involving significant employee hands-on effort, the packing and preparation stage is often a key area where errors occur. Being able to quickly scan, check, record and document goods and shipments, with barcode or RFID enabled labels, allows operators to manage the finished goods process flow efficiently.
Automating the fulfillment process, through the adoption of SATO mobile, desktop and industrial intelligent label printing solutions drives accuracy, productivity, traceability and compliance with the latest regulations.
With wireless mobile printers designed for the warehouse environment, operators are free to focus on the packing process and then complete final checks at the point of shipping to ensure complete accuracy in matching goods, transportation and destinations.
See SATO Solutions
Cross docking
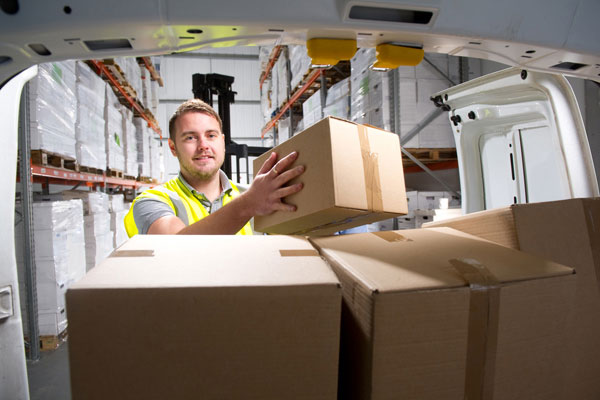
First developed as a logistics process in the 1950s, cross docking is the practice of unloading materials from incoming transport and directly loading the goods or materials into an outbound vehicle immediately, with little or no storage in between. Sometimes used to save time in the receiving and redistribution process, cross docking is a sensitive process that can result in confusion, waste and errors if not managed correctly.
Ensuring packaging and pallets are on the right transport, in the right order, and destined for the correct location, means real-time accurate data is required to create transparency and visibility of all activities.. Real-time location management of products, assets and employees can enhance cross-docking productivity, minimise errors and ensure customer service satisfaction is maintained.
The latest innovative labelling solutions from SATO help minimise cross docking errors. Employees receiving incoming goods can log them in to an inventory control application, using desktop, industrial or mobile printers to generate a barcode shipping label, with the appropriate cross docking information, and ensure the right goods, go in the right transportation to the right destination; on time, every time.
Accurate point-of-activity labelling facilitates the free flow of goods and eliminates the need for manual, error-prone processes. No label searching, or time-wasting comparisons of bills of lading are required, as pallets are loaded and barcodes or RFID tags are scanned to confirm the right shipments are in, and going, to the right place.
SATO provides users with tools for visibility and operations transparency to meet the demands of the busy logistics operation keeping compliance and safety at the forefront of the cross-docking management solution.
See SATO Solutions
Shipping control
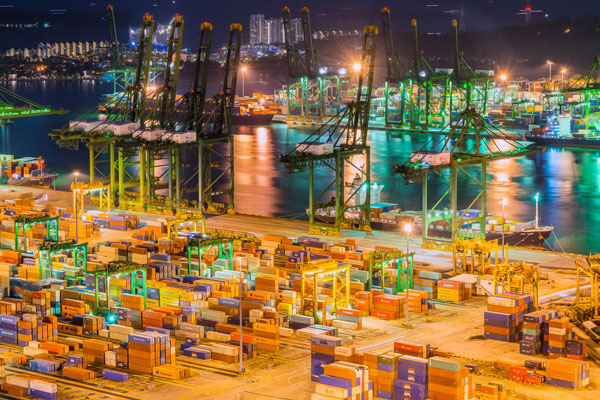
From cosmetics to coconuts, furniture to footballs, control of shipping processes demands accurate, real-time, measurable data to verify processes have been accurately applied, goods are going to arrive in the correct destination and customers are going to be satisfied.
Automation of the final shipping process is necessary to minimise human error. Elimination of manually created documentation and hand written labels enables timely verification of goods being in the right transport. This drives productivity, as well as avoids loss of time in unloading and reloading of trucks. Finally shipping space allocation and transport can be optimised resulting in a reduced number of trucks, railcars or trailers being booked and lowering of ultimate costs.
SATO, a leader in auto identification and data collection technology for the transport and logistics sector, has a range of solutions to add value and drive productivity in the warehouse and shipping environment.
SATO’s mobile and fixed printing solutions, scanners, barcode labels and RFID tags provide a comprehensive capability to provide operators with the automation required to effectively track and verify shipping processes from dispatch to transport allocation and maximise space utilisation.
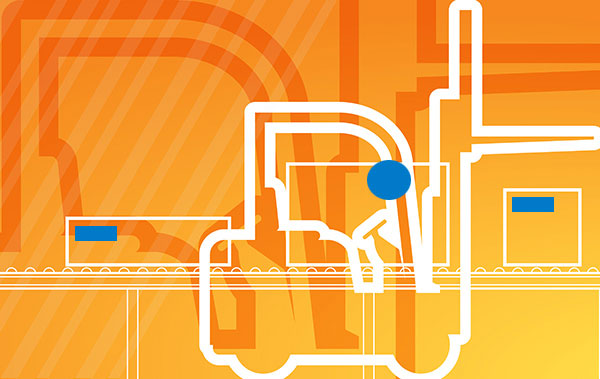
An example: A Forklift Compatible System
A forklift compatible system provides both picking and shipping labels to improve shipping operations. It comprises a small mobile thermal printer, which can be mounted on to any forklift, and a handheld terminal with integrated LCD screen. When a new order is received, the driver scans the warehouse shelf label and then the barcode on the product. This information is communicated to the host computer. If the product and location are correct, the host automatically sends a shipping label instruction to the SATO thermal printer on the forklift, confirming that the label and picked item match, which can then be printed out, real-time in the middle of the warehouse, ready for shipping.
See SATO Solutions
Reverse logistics management
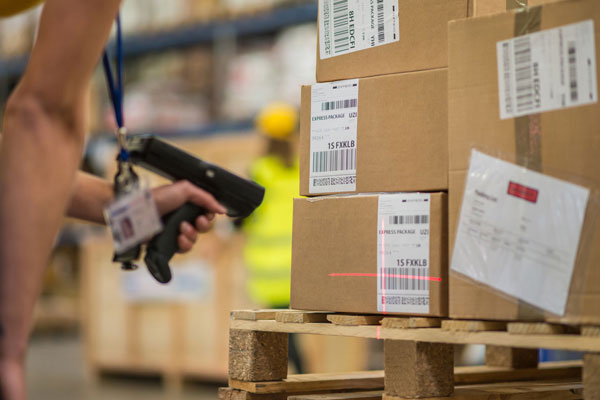
With the explosion in consumer online retailing and e-commerce in recent years, reverse logistics, the process of planning, implementing and controlling the efficient inbound flow of returned secondary goods and related information, is a huge challenge to transport and logistics operators.
Often more complex than normal distribution processes, the shipping and packing compliance requirements, on top of the large number of items moving back and forth in the supply chain, create clear challenges for productivity, costs and waste management.
Brands and retailers seek speedy resolution to consumer returns to protect customer satisfaction and brand loyalty, as well as quick re-entry into inventory to minimise loss of value and enable the sales process to restart. Businesses need real time visibility of product locations and status to enable efficient processing, inventory re-entry management and identification of goods for disposal. Being able to automatically record product condition upon receipt enables proactive decision making on the restocking, refurbishment or disposal of goods. Efficiency can also be gained in returning unused goods to the manufacturing process and minimise unnecessary reordering. Finally, today’s stringent regulations increasingly require that traceability information is available to demonstrate safe handling and monitor hazardous material handling where required.
All of these needs drive demand for SATO auto identification and data collection solutions in the transport and logistics sector. As a leader in best in class labelling solutions, SATO supports operators to create and manage seamless reverse logistics processes.
Whether a manufacturer, retailer or e-commerce company, SATO provides a comprehensive range of mobile, desktop and industrial printers with complementary labels, scanners and accessories, to integrate into logistics operations enabling efficient processing of customer returns, the required visibility for efficient decision making, as well as adding value and profitability to the operation wherever possible.
See SATO Solutions

Contact us
